|
Свойства автомобильных стёкол
С тех пор как научились варить стекло, его химический состав не претерпел серьезных изменений: та же смесь кварцевого песка и щелочи, сплавляемая при температуре около 1300° С. На ранних автомобилях стекла по существу не отличались от обычных оконных. И хотя оптические свойства материала были вполне приемлемы, сразу стало ясно, что он слишком хрупок: при ударе его острые осколки способны опасно ранить. Искали заменители. Целлулоидная пленка не годилась по оптическим свойствам, к тому же быстро старела, отчего еще более ухудшалась ее светопроницаемость. В 30-е годы, когда появился плексиглас, казалось, что это решит все проблемы. Но он быстро мутнеет - подхваченные потоком воздуха, обтекающим машину, частицы пыли вызывают быстрый абразивный износ. Поэтому технологи и ученые продолжали работать над тем, чтобы обеспечить стеклу нужное сочетание оптических и механических свойств.
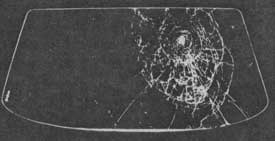
Таи выглядит после сильного удара лобовое стекло из триплекса. |
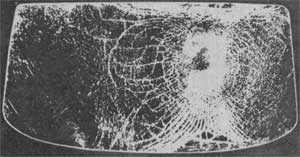
По характеру разрушения стекло "тен-твенти" напоминает закаленное, но его осколки остаются на пленке. |
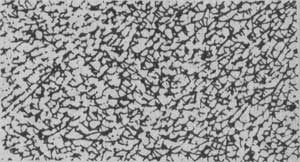
Закаленное стекло от удара разрушается на множество частиц, примерно одинаковых по размеру. |
Получить безопасное стекло, как это часто бывает, помог случай. В 1903 году французский химик Э. Бенедиктус уронил на пол стеклянную бутылку. Она неожиданно осталась целой, хотя и покрылась сеткой трещин: осколки удерживала пленка, образовавшаяся на внутренней поверхности от давно испарившегося содержимого.
Курьез натолкнул на идею трехслойного стекла "триплекс". Гораздо прочнее обычного, оно все же не стало вполне безопасным: после сильного удара триплекс покрывается сеткой трещин, теряет прозрачность и дает осколки с острыми кромками. Тем не менее сегодня почти все легковые и грузовые автомобили комплектуют лобовым стеклом именно такого типа, что закреплено законодательными требованиями многих стран по безопасности.
Правда, современное многослойное стекло отличается от первых материалом промежуточной пленки. От применявшегося вначале целлулоида отказались: под действием солнечных лучей он становится коричневым и пропускает гораздо меньше света. В 30-е годы использовали ацетатную целлюлозу, но пленка из нее, в свою очередь, мутнеет. После войны был синтезирован более стабильный материал - поливинил-бутирол (ПВБ).
Новые проблемы перед технологами поставили дизайнеры, предложившие делать лобовые, задние, а позже боковые стекла не плоскими, а гнутыми. Этого достигают методом так называемого свободного моллирования. Два плоских листа толщиной около 3 мм укладывают на форму и помещают в электрическую печь. При соответствующей температуре они размягчаются и под действием собственной массы облегают форму, приобретая необходимую конфигурацию. Затем между стеклами прокладывают пленку и, чтобы "склеить" их воедино, тщательно удалив оставшийся воздух, устанавливают этот "сандвич" в автоклав, где поддерживается температура порядка 140°С и давление около 7 кгс/см2.
Закаленные стекла появились в 1932 году. Как и некоторые другие, этот способ изготовления стекла уходит корнями в далекое прошлое. Некогда было замечено, что, если капнуть расплавленным стеклом в воду, получаются очень прочные грушевидные капли - их с трудом удается разбить молотком. Если же отколоть кусочек от "хвоста" груши, остальная ее часть рассыпается в мелкий порошок.
Для закалки стекло интенсивно охлаждают воздухом после выхода из печи моллирования, и в его наружном слое возникают сжимающие напряжения, а во внутренней зоне - растягивающие. Это резко увеличивает прочность стекла на изгиб. Под воздействием изгибающей нагрузки наружные слои растягиваются, но оно не разрушается до тех пор, пока напряжения в этих слоях не превысят остаточных напряжений от термообработки. Действие внутренних сил упругости обусловливает и высокую прочность закаленных стекол - в шесть раз большую, чем у обычных. А при разрушении они дают множество осколков - мелких, с тупыми кромками и потому практически безопасных.
Хотя, как уже сказано, ударная прочность закаленных стекол очень высока, изменение микроструктуры поверхностных слоев иногда может вызвать увеличение размеров кристаллических зерен, что порой приводит к внезапному и внешне совершенно беспричинному разрушению. Это свойство закаленных стекол в совокупности с большей, чем у слоистых, потерей прозрачности при ударе является их недостатком. Но следует иметь в виду, что закаленные стекла втрое дешевле.
Специалисты пытаются, и не без успеха, улучшать характеристики как закаленных, так и многослойных стекол. Совершенствуя воздуходувки, обеспечивают так называемую зонную закалку, в результате которой при аварии стекло перед глазами водителя растрескивается на более крупные частицы, оставаясь относительно прозрачным.
Закаленное стекло практически не поддается механической обработке, поэтому операцию закалки проводят последней - после придания заготовке нужной формы и размера. Интересно, что очень долго не умели получать лист постоянной толщины с гладкой поверхностью. Только в 1959 году был разработан такой процесс: стеклянная лента, полученная из расплава, проходит через печь, как бы проплывая по поверхности расплавленного олова с постоянной температурой. При этом все неровности оплавляются и сглаживаются о поверхность олова.
Что касается триплекса, то с развитием технологии научились обеспечивать столь высокое сцепление стекла с пленкой, что при разрушении осколки практически не отделяются от нее. Не удовлетворившись, инженеры разработали новый тип безопасного стекла: "тен-твенти" ("десять-двадцать"). У него наружный слой из обычного, а внутренний - из термообработанного материала. Так удалось добиться значительно лучшего, чем у триплекса, сочетания оптических свойств и безопасности. Однако новое стекло получилось в несколько раз дороже, поэтому его ставят только на дорогие автомобили за отдельную плату.
Следующим шагом стало четырех-слойное стекло "секьюрифлекс". В его основе - известный нам триплекс, на внутреннюю поверхность которого нанесена тонкая пленка специальной пластмассы. Она-то и страхует против отскакивания осколков внутрь салона.
А теперь, как это часто бывает, инженерная мысль двинулась в другом направлении - к упрощению конструкции безопасных стекол. Всерьез задумываются, не заменить ли сверхбезопасное четырехслойное, скажем, двухслойным.
Но было бы неверно думать, что заботы автомобилестроителей связаны только с безопасностью окон. Есть и другие: с
увеличением площади остекления (а эта тенденция устойчива) в салон проникает все больше солнечного света и,
значит, тепла. В жаркую пору пассажиры ощущают их избыток. Выходом стало применение атермальных стекол, поглощающих значительную долю (до 40%) инфракрасных лучей. Эффект достигается добавкой в сплав окиси кобальта, которая придает стеклу голубовато-зеленую окраску. Если же ввести окись железа, цвет станет бронзово-серым. В последнем случае тепло поглощается значительно слабее, но автомобиль с "бронзовыми" стеклами выглядит, пожалуй, эффектнее.
Электрообогреваемые стёкла изготовляют, нанося силикатно-серебряную токопро-водящую пасту через специальный шелкотрафареткый экран. Получаемая сетка несколько ухудшает видимость, поэтому для лобовых стекол такой способ неприемлем. Но уже разработан другой: при помощи тончайших (0,01 мм) вольфрамовых нитей. Такие проводники совершенно незаметны для глаза.
Таким же образом на внутреннюю поверхность лобовых стекол наносят антенны. Однако подобно обогреваемым лобовым
они сегодня еще дороги и редки.
o Как видим, прогресс в конструкции автомобиля во многом коснулся стекол. Большую роль здесь играет дизайн, развитие формы кузова. В последние годы широко распространились гнутые стекла для боковых окон. Многими фирмами решена и такая задача, как установка стекол (в первую очередь лобовых и задних) заподлицо. Их не вставляют в уплотнитель, а вклеивают в проем. На ряде моделей "зализаны" с поверхностью и боковые стекла. Конечно, конструкция двери и уплотнителя в этом случае отличается от традиционной.
Аэродинамически совершенный стиль кузова обладает не только эстетическими, но и практическими достоинствами: улучшается экономичность автомобиля. Другой резерв ее - снижение массы. Этому помогают облегченные (более тонкие) стекла. За последние годы толщина закаленного листа в мировой практике уменьшилась с 5,5 до 4 мм. Реально довести ее до 3,2-3,0 мм. Тоньше стали и многослойные стекла: около 5 мм вместо прежних 7 мм.
Поскольку утонение не должно сказаться на прочности, возникают проблемы при формовании и термообработке. Кроме того, в кузове с тонкими стеклами выше уровень шума и вибраций, что может потребовать увеличения массы шумопоглощающих мастик.
Тем 'не менее переход на стекла уменьшенной толщины помог снизить массу некоторых машин на 9-12 кг. Выгода очевидна, и потому тонкие стекла применяют все шире. В частности, ими будут комплектоваться и новые модели наших легковых машин.
Развитие конструкции автомобиля проходит под знаком все более высоких требований к его экономичности, безопасности, комфортабельности. И для их удовлетворения понадобится внести еще много нового в конструкцию и технологию производства стекол.
|
|